Aluminum Scrap Markets
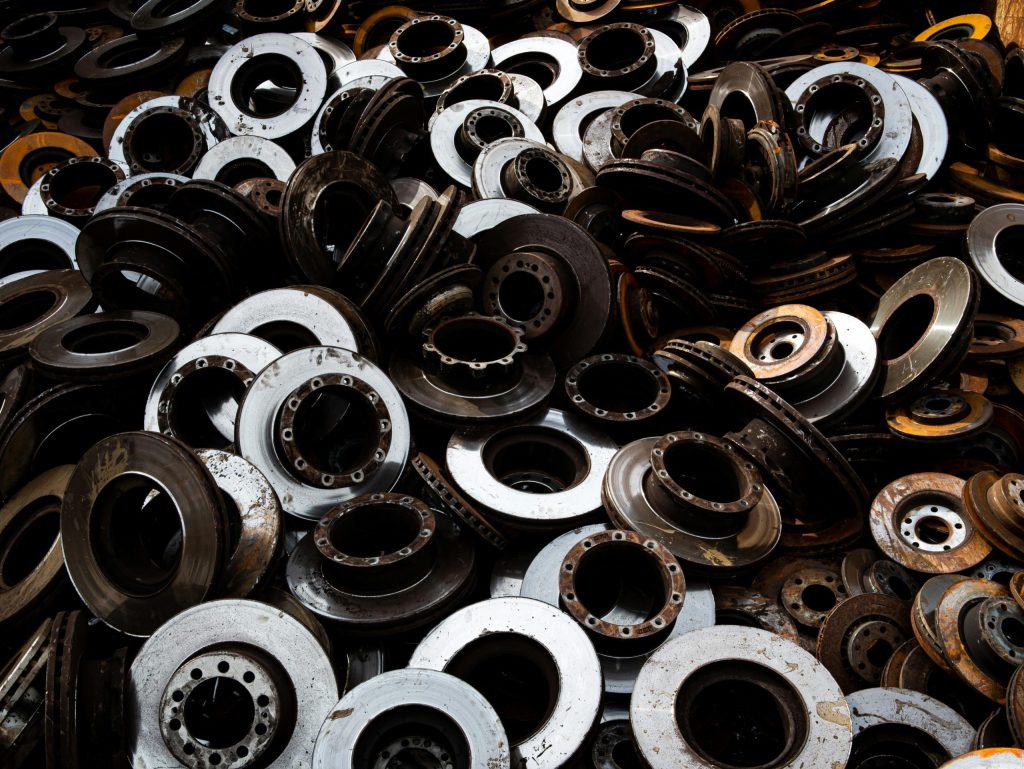
30 June 2025
Casting a wider net: Cascade Die Casting to expand North Carolina site
Written by Nicholas Bell
Cascade Die Casting (CDC) plans to expand operations at the company’s High Point, North Carolina operation.
The company is investing $8 million into its “Atlantic Division”, comprised of a couple of facilities, with additional support from the local City of High Point and Guilford County to boost infrastructure capacity.
CDC Atlantic already houses 13 die-casting machines (ranging from 900 to 1,600 tons), three on-site furnaces, and shot blasting capabilities.
In 2021, it melted more than 10 million pounds of aluminum – over 4,500 metric tons – even during a period marked by supply chain bottlenecks and a subdued automotive market.
That level of output drawn from a likely underutilized year, signals that the nameplate capacity could be even higher.
Adding notches to a manufacturing belt
CDC’s High Point plant is well-placed within a North Carolina industrial pocket.
Daimler North America’s Thomas Built Buses’ manufacturing site is just down the road, and other key Daimler subsidiaries – including a Gastonia Components operation and Freightliner’s largest manufacturing plant – are within reach as well.
Caterpillar has nearby plants in Winston-Salem, Clayton, and Sanford, and GKN’s automotive footprint is almost exclusively within a couple of hours of CDC Atlantic.
In short, Cascade is in the right operating radius, even if the hub’s stated purpose is to serve the southeastern region of the U.S. as well as Mexico.
Where A380 and A413 fit
CDC Atlantic exclusively casts A380 and A413 secondary alloys, both die-cast grades synonymous with the automotive market.
No alloy is more emblematic of the secondary casting market than A380, while A413, by contrast, serves a more niche role, commonly used in cylinder head and piston production as well as other high-pressure hydraulic applications.
U.S. A380 output topped 200,000 metric tons in 2024, according to the U.S. Geological Survey, compared to A413 which fell under a broader category of secondary die-cast alloys representing about 13% of die-cast production over the same period.
CDC’s implied melting capacity would place it close to 1.5-2.0% of national die-cast production, excluding sand and permanent mold processes, with output trending towards the upper end of that range. While 2% may sound modest, when spread across more than 225 casting sites in the U.S., it’s a meaningful slice – especially considering the figure is likely a conservative estimate, with actual throughput potentially exceeding those totals.
Cascade’s bet on High Point reinforces the trend that scrap-fed die-castings are still a prevalent part of automotive aluminum, despite recurring bottlenecks and muted production levels. The High Point facility, in particular, is also strategically positioned within a manufacturing corridor dense with OEMs that service the commercial vehicle sector – arguably the segment where light-weighting remains a top design priority.