Aluminum Scrap Markets
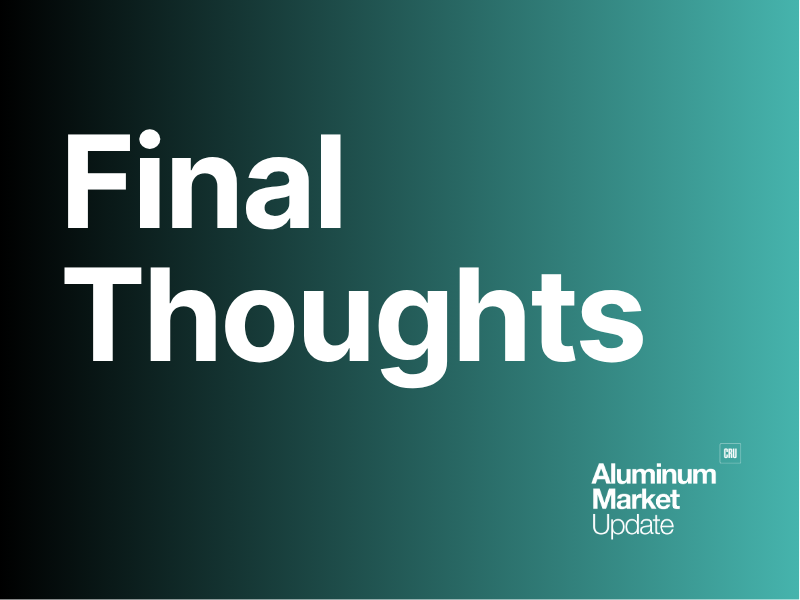
24 July 2025
Gears in motion: American Axle & Manufacturing and Dowlais merger
Written by Nicholas Bell
July 15 marked a significant milestone in the North American auto parts supply chain that flew largely under the radar.
American Axle & Manufacturing (AAM) shareholders voted to advance its acquisition of UK-based Dowlais Group PLC, parent company of driveline heavyweight GKN Automotive and powder metallurgy specialist GKN Powder Metallurgy.
This merger-of-equals clears the last hurdle for combining two major Tier 1 suppliers. The timing was fortuitous – the announcement of the merger came before 25% tariffs on imported auto parts imposed by the Trump administration, and the overwhelming vote in favor of the merger occurred after the duties took effect.
More importantly, the tie-up between AAM and Dowlais signals an inflection point for aluminum usage in vehicles, regional scrap flows, global supply chain exposure, and the evolving economics of internal combustion engine vehicles (ICEs) and electric vehicles (EVs).
Two footprints from one step
The deal creates one of North America’s largest auto part suppliers by revenue, and the fourth largest when excluding non-mechanical suppliers like seat manufacturers and electronic specialists.
AAM will pay roughly $1.44 billion in cash and stock for Dowlais, bringing together two “complementary global Tier 1 suppliers” and forming “one of the leading global driveline and metal forming companies” with greater scale.
AAM contributes 24 U.S. manufacturing locations, including a dozen in Mexico, to the fold, while Dowlais adds 18 manufacturing sites in the U.S., with three south of the border.
Many of these facilities cluster in the Midwest and Pennsylvania, with both firms heavily concentrated around Guanajuato, Mexico.
In fact, some AAM and GKN factories are practically neighbors, less than an hour’s drive apart or located in the same cities, which could yield consolidation opportunities.
Dowlais’ differential advantage
Outside of geographic overlap, the new entity diversifies the customer base dramatically. More than two-thirds of AAM’s 2024 sales were generated from the domestic Big Three auto manufacturers – General Motors, Ford Motor Group, and Stellantis.
Meanwhile, GKN Automotive (Dowlais’ core automotive division) derives sales from the likes of Toyota, Volkswagen, and Renault-Nissan, with half of their revenue coming from a broad “other” category that includes numerous China-based electric vehicle upstarts and other legacy assemblers based in Asia.
In fact, about 50% of all passenger vehicles worldwide contain at least one GKN driveline component, whether that includes constant-velocity joints, side shafts, or any other of their offerings.
The merger will provide the combined company with inroads to nearly every global automaker, while creating a “powertrain agnostic portfolio”.
Strategically, AAM’s and Dowlais’ products complement each other.
AAM is known for axles, drive shafts, aluminum valve bodies, gear housing, and forged metal components. GKN Automotive provides structurally supportive half-shafts and electric drive units, and GKN Powder Metallurgy contributes precision metal components.
Together the company will be able to offer ICE and EV drivetrain components to both North American and non-North American auto manufacturers.
The transfer case
The consolidation’s prospectus underpins an uncertain future that challenges strategic planning across the automotive supply chain.
Regional EV adoption rates vary widely: China is moving fast to transition to a EV passenger market, but the U.S. is slow to shift its preference.
It’s not just the pace of EV adoption, whether driven by consumer preferences or government tax credits, that’s shifting the landscape. It’s the parts each category of vehicle contains.
The evolution of drivetrain manufacturing is a critical juncture, particularly for aluminum demand.
Historically, the most aluminum-intensive parts of an passenger vehicle, after the engine block, is the drivetrain system. According to a Ducker Carlilse’s 2020 analysis, aluminum content in drivetrain systems accounts for an average of 85-86 pounds per vehicle.
And unlike increasing aluminum content in other parts, like wheels, body components, subframes, that aluminum content isn’t projected to increase anytime soon (there was no change in the 2020 analysis’ figure and its 2026 projection).
As the industry shifts toward electrification, the nature of aluminum usage is more evolving, rather than increasing or disappearing.
Battery electric vehicles (BEV) eliminate many traditional cast aluminum parts. It’s increasingly common for an electric vehicle to have no traditional multi-speed transmission, driveshafts, and differential carriers altogether.
Yet EVs introduce aluminum-intensive systems in their place: motor housings, gearboxes, power electronics enclosures, and structural components need for lightweight purposes.
A merger cast in aluminum
AAM and Dowlais’ combination represents a meeting of legacy-driven U.S. internal combustion engine vehicle markets of AAM and Dowlais’ casting versatility and global customer reach, especially in the burgeoning electric vehicle and Chinese markets.
It also unites North American manufacturing among Tier 1 suppliers at a moment when regionality, content traceability, and feedstock sourcing are under increasing scrutiny, even as it was set in motion months prior to today’s protectionist U.S. economy.
Either way, the new entity will expand the impact on suppliers further upstream.
From Tier 2 suppliers providing semi-fabricated products like secondary smelters or billet producers or extruders, to Tier 3 sources that sit at the raw material starting point of the circular ecosystem like scrap dealers/processors and possibly even primary aluminum in some cases, the new behemoth auto part company will have reverberations throughout the supply chain.
While the aluminum footprint of a drivetrain is measured in pounds, collective scrap generation across three dozen manufacturing plants adds up fast. Look out for Part 2 of this story on our website and in AMU’s Pulse Weekly newsletter Wednesday.