Global Trade
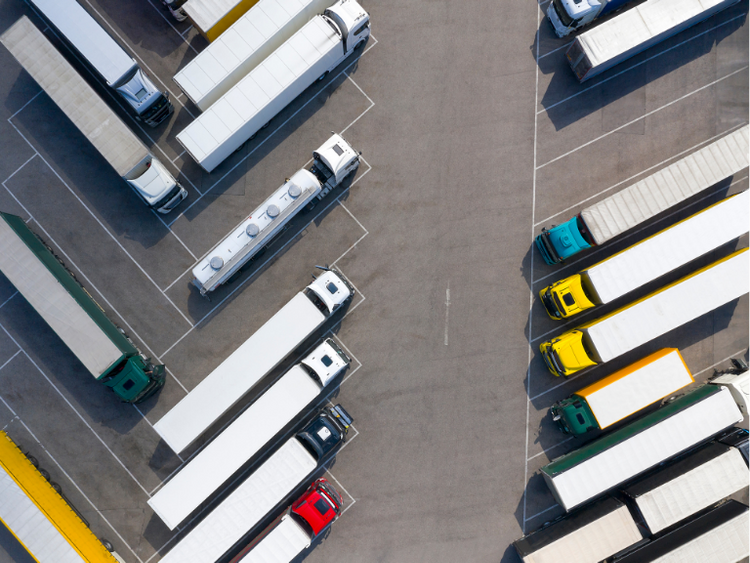
22 July 2025
Trucks, trailers, tariffs: Updated commercial vehicle data
Written by Nicholas Bell
A brief surge in June trailer orders offered a flicker of optimism, but the commercial vehicle market remains stuck between softening freight activity and rising input costs, particularly for aluminum-intensive products.
OEMs are struggling to maintain pricing power, body builders are absorbing disproportionate inflation, and fleets are waiting out uncertainty by extending equipment lifecycles or shifting to rentals.
Tariffs and fabrication costs are inflating nominal pricing, but true demand signals remain inconsistent and fragile for aluminum suppliers in this fractured landscape.
Trailer orders rebound amid weak fundamentals
U.S. trailer net orders more than doubled month-over-month in June, rising 113% to 13,827 units and reversing a sharp drop in May, according to FTR Transportation Intelligence.
While the year-over-year gain of 157% also appears dramatic, it’s measured against one of the weakest Junes on record since FTR began tracking in 2013.
Order cancellations fell from a steep 39% in May to a more typical 17% in June. Despite the order uptick, cumulative orders for the 2025 build season (September 2024-June 2025) reached 175,242 units, down by 5% year-over-year.
Build rates continue to outpace new orders, a trend carried over from May.
June builds rose by 7% month-to-month to 18,071 units, shrinking order backlogs by about 4% to 104,219 units. That left an output-to-order surplus of 4,200 trailers.
Trailer build rates fall sharply on the year
Year-to-date build rates reflect an ever-steeper drop in output. Total trailer builds in the first half of the year fell by 26% to 98,773 units, which also pegs the monthly average a little bit higher than June throughput at 16,462 units.
FTR Senior Analyst for Commercial Vehicles Dan Moyes noted the jump in tariffs to a 50% rate from 25% in June are already elevating production costs and putting downward pressure on original equipment manufacturer (OEM) demand.
“OEMs and suppliers face pressure to either absorb rising costs or pass them on to fleets,” Moyer said.
Class 5-8 trucks exhibit broad softness
The softness in the trailer market mirrors deeper weakness in the Class 8 trucking sector that tends to tow them.
Final June North American Class 8 net orders were at just 9,463 units, down 35% year-over-year, as the for-hire freight market enters its thirteenth quarter of recession, according to ACT Research.
Class 5-7 truck orders, which contain a larger share of medium-duty commercial vehicles, fell even harder, down 40% year-over-year to 12,387 units. Vocational truck orders, which commonly fall under the Class 5-7 truck distinction, were down 23% on an annual basis, facing downward pressure weak construction sector and housing market demand.
FTR pegged preliminary Class 8 net orders even lower at 8,900 units, a monthly drop of 25% and 36% annual decline from their 2024 data and the lowest going back to 2009.
FTR’s Moyer highlighted that anticipated revisions of the EPA’s 2027 nitrogen oxide (NOx) emissions standards have become a growing cause of uncertainty, though elsewhere they were not the most often cited extenuating factor.
OEMs confirm the downshift
Recent Q2’25 earnings from top commercial manufacturers reinforce the theme.
PACCAR, parent company of Peterbilt and Kenworth, reported an 8% decline in U.S. and Canadian truck deliveries, totaling 10,800 units, in their earnings on July 22.
Chief Executive Officer Preston Feight acknowledged while demand remains strong in some vocational and less-than-truckload segments, the soft truckload market and tariff drags are weighing on North American performance.
Meanwhile, Volvo also posted a 20% year-over-year decline to 12,981 units in quarterly North American deliveries on July 17, a steeper decline than its company-wide figure across all regions. Similarly, as worldwide global net order intake at Volvo Q2’25 differed by just one unit, North American orders fell by 15%-16% over the same period.
Fleets staying put
Utilization data further confirms a fragile ground freight backdrop cited by OEMs.
Seven-day volumes for the weeks ended July 4, 11, and 18 were only above average on any given week across seven different states, while the rest of the country was flat- to below-average multiple weeks by half to two-thirds of the continental U.S.
Weekly spot volumes over the same periods were often 20%-60% below normal in many states.
PPI data magnifies a margin squeeze
Producer price index (PPI) data for June reveals a layered inflation dynamic across the vehicle and trailer supply chain.
A recent AMU analysis of aluminum PPI data for June mirrors trends in the commercial vehicle sector and can be taken a step further.
PPI data also indicates trailer body builders and fabricators are being squeezed by outsized upticks in midstream price data. Truck and bus bodies (+4.8% YoY), dump truck bodies (+5.8% YoY), and service truck bodies (+6.7% YoY) have all seen higher price surges than finished trailers themselves (+1.8%).
These figures suggest midstream fabricators are still absorbing cost pressures from prior surges in raw materials from further upstream, like aluminum, while struggling to pass them on fully.
Meanwhile, price inflation in truck, trailer, and RV rental and leasing, which was up year-over-year by 6.2% in June and posted spikes above 1% on month-to-month bases in April and May, prior to a relatively flat June.
Upstream flows downstream
Given the high cancellation rates in May and ongoing backlog softness, many fleets appear to be holding off on new builds, opting instead to lease or extend the use of existing trailers, depending on where they sit in the value chain. The trend further indicates the view that buyers are waiting out tariff uncertainty before committing to a fresh fleet.
While June’s trailer order surge hints at stabilization, the surrounding data tell a more nuanced story. The aluminum market faces a bifurcated ecosystem where tariffs and fabricated input costs are keeping nominal prices high, but true demand is uneven from final product segments.
Falling build rates, backlog erosion, on-the-ground freight sluggishness, and weaker OEM deliveries continues the pattern of price hikes trickling down the supply chain, hitting folks further downstream one step at a time.